Reasons Deburring is Crucial
Last week we established that burrs can cause problems to your workforce, your production efficiency, your machinery, and your final product. Let’s look more deeply at why it’s such an important topic.
Workplace Safety: We have all heard about safety first, but that’s because it is the cornerstone of the workplace. Injuries not only hurt the employee but also impact costs in multiple ways such as sick pay, decreased output, lost time, overtime, and insurance. There were almost 60 thousand cuts and lacerations reported in the workplace in 2020[i]. Removing burrs will reduce the frequency and severity of lacerations to your employees and the cost to your bottom line.
Overhead costs/machinery life: Just as burrs can hurt your workers, burrs can also damage machinery. If burrs are not removed, they can dislodge and cause clogs or wear in the next machine downstream in your line. Excessive and unplanned capital expenditures impact profits. Extending the life of your machinery saves you from downtime, unexpected costs, and the headache of repairs.
Longevity: Burrs can break off and shorten the life of the part (and the machine housing that part). Again, this can impact your business financially – but there are also more serious consequences to faulty parts. For example, if a part inside an engine is not properly deburred, that burr can come loose and cause failure to the entire engine. Burrs can also cause heat (via friction), potentially compromising the part. This opens up new risk in terms of liability, quality, and more.
Precision: Workpieces are designed to exacting measurements for high-level performance. Burrs keep pieces from fitting and working properly and can result in rejected parts. And if you can’t make quality products, you’re not going to be selling any products. Tight tolerances and precise specs don’t leave room for error.
Specific industry needs: There are many use cases where burrs would truly cause critical issues. The food industry must exercise serious caution to ensure tiny metal pieces don’t end up in products consumers eat and drink. Medical or surgical implants and devices also have exceptionally high standards because rough metal edges could lead to internal damage or a legitimate biological hazard. And in the aerospace and automotive industries, burrs can lead to equipment failure, injury, liability and more.
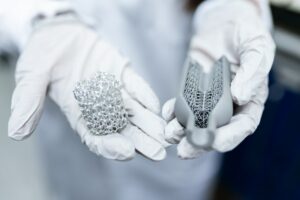
Photo by ThisisEngineering RAEng on Unsplash
Making sure your parts are burr-free is essential to the safety of your workplace and your bottom line. In the end, the deburring method you choose will depend on the category and properties of the burrs you are trying to remove. We’ll start looking at those categories and properties in next week’s installment. To truly understand what a deburring process can do for you, parts should be tested by the machine builder so you can discuss the results for a smooth collaborative relationship.
The primary reasons to deburr are clear: to produce parts that are less prone to quality issues or failure, to lower the risk of injury to your team or end users, and to protect equipment and aspects of your production process downstream.
COMING UP Next: Burrs by Machining Process
I U.S. Bureau of Labor and Statistics, 2020 TABLE R31. Number of nonfatal occupational injuries and illnesses involving days away from work by event or exposure leading to injury or illness and selected natures of injury or illness, private industry, 2020