Last week we looked at the five classes that encompass most burrs. This week we are exploring the many common deburring methods that are frequently considered for removal.
There are many options for deburring; manual vs. mechanical, with or without chemicals or solvents, explosive methods, grinding, tumbling, the list is extensive. The key is to determine the best method to deburr. Some factors include the type of burr, the location of the burr, the quality required of the finished product, where the burr is formed within the machining process, and of course, cost.
You will note that we are focusing on mechanical removal options below. There are of course cases where deburring can be done manually, but the outcomes will have slight differences every time. With the proper automated machine-based deburring approach, you can achieve repeatable, precise results over and over.
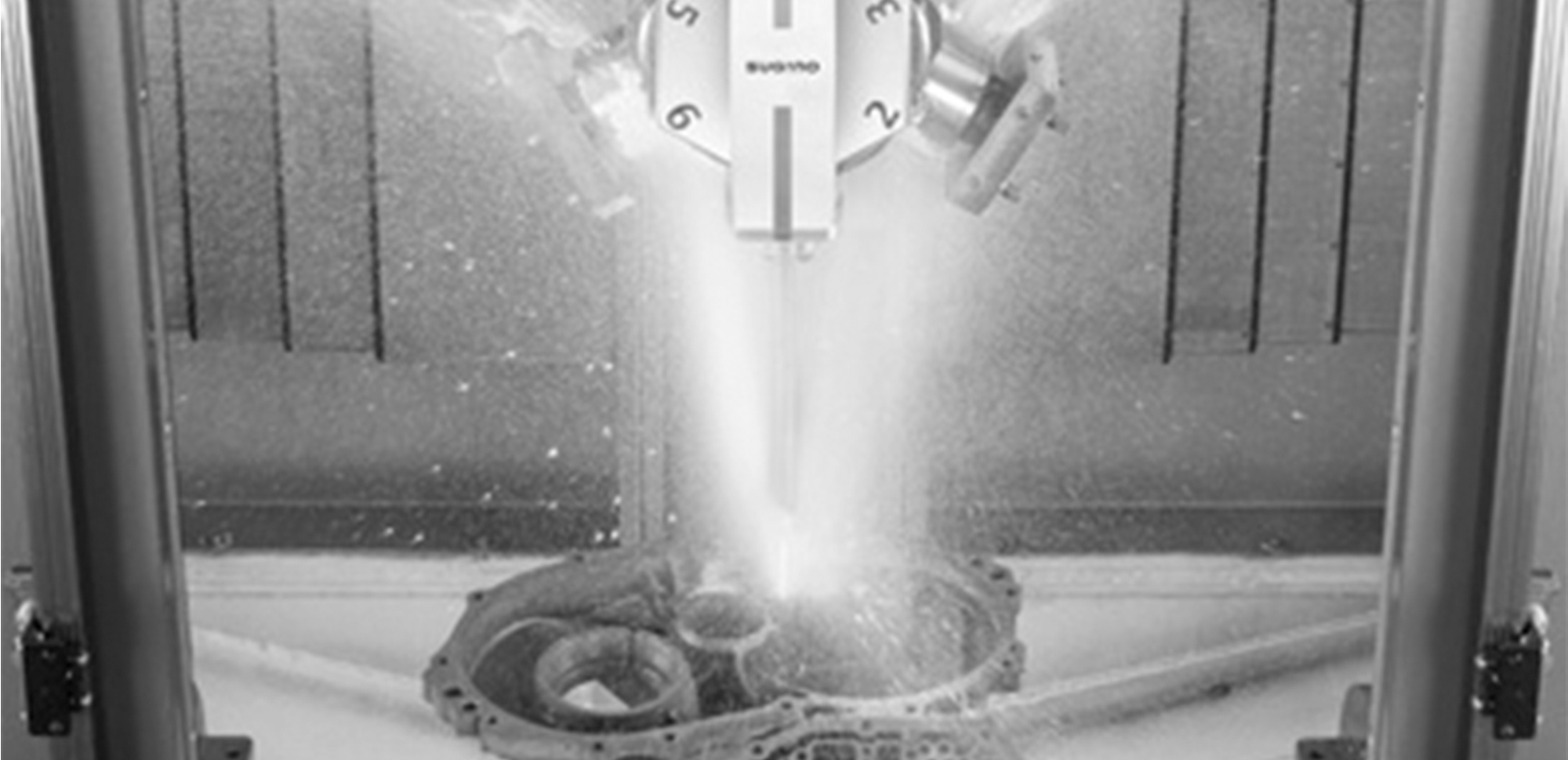
Sugino’s High Pressure Water Jet Deburring and Cleaning Systems
Water Jet Deburring
One of the main benefits of water-jet deburring is a high level of precision and repeatability – and for this reason, CNC control is used. This eco-friendly process uses high-pressure water to remove loose burrs and chips even in deep holes – all while leaving the parts cleaner and free of debris. Note: We’ll be covering waterjet deburring in-depth next week so make sure to follow along.
Mechanical Deburring
.jpg)
Sugino’s Barriquan Self Compensating Deburring Tool
Cutting, grinding, milling, or brushing tools remove burrs through direct contact.
Rotary Tool
Deburrs by a rotating tool with a special protruded edge. This can be made more efficient by mounting on a machining center or CNC lathe.
Belt Polishing
Abrasive cloth paper is rotated to remove burrs with abrasive grains while polishing. Large burrs can be removed efficiently, but burrs inside the workpiece or within intersecting / cross holes are not accessible. This method can also result in secondary burr formation.
Electrochemical Deburring
Small burrs are broken down and removed via an electrolyte solution (generally saltwater) and an electrical current.
Brush Polishing
Brush polishing employs various-shaped brushes (wheel, roll, cup, spiral, etc.) to remove burrs. These can be mounted on a machining center or CNC lathe.
Barrel Polishing
The part to be deburred is tumbled within a rotating barrel. This can run with or without water and with or without an added abrasive medium.
Thermal Deburring
Fuel gas and oxygen are combusted under pressure. The resulting explosion incinerates the burr into oxidized powder.
Chemical Deburring
Micro-burrs are dissolved using a phosphoric acid-based or sulfuric/fluorine-based solution.
As you can see there are a lot of options to remove your burrs, and each option has benefits and drawbacks. Often, the best way to find your deburring match is to have your parts tested to determine the ideal method. One that applies specifically to your production issues and works seamlessly into your manufacturing process.