Machining with a lathe has unique challenges.
Inconsistencies in surface roughness
Shortened life for cutting tips
Adding a grinding process with another machine
Superoll™ is the answer.
ROLLER BURNISHING
What is Superoll?
Superoll is a full line of roller burnishing tools that create smoother finishes through compressing the surface - without removing material.LEARN MORE
Explore example case studies
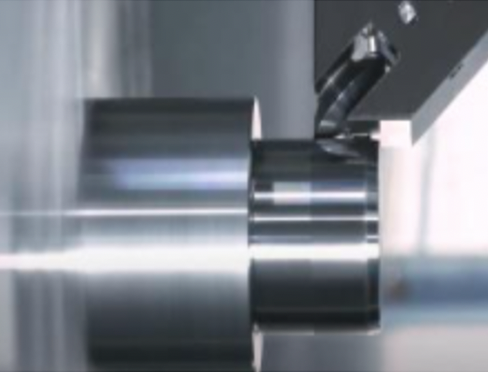
Quality and Precision
These hardened and highly polished tools integrate into machining centers to eliminate secondary processes such as grinding and honing, without removing any material.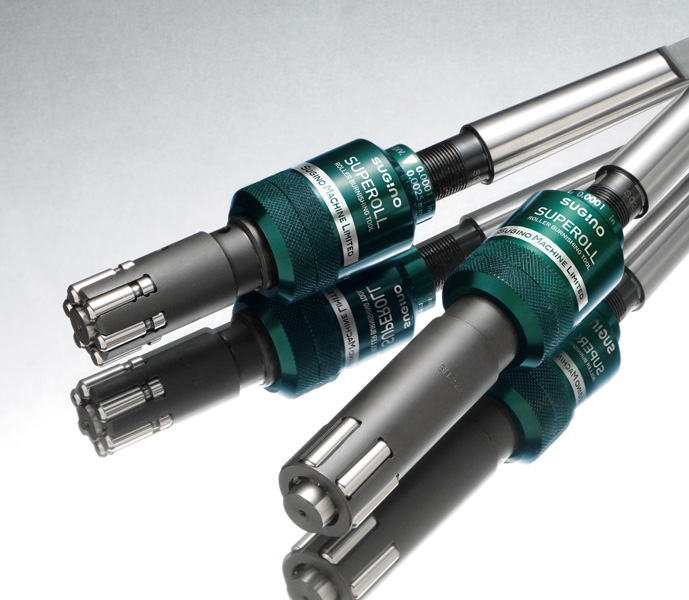
A Mirror-Like Finish
Ideal for processing with shorter cycle times to improve productivity and reduce costs.Comparing Conventional Methods with Using Superoll in your Lathe
Rough Machining + Dimensional Finish + Surface Finish
Lathe Machining the Conventional Way
The conventional way involves rough machining with a cutting tip first, then dimensional finish. From there, a separate process and machine is often needed to achievee the desired surface finish result.
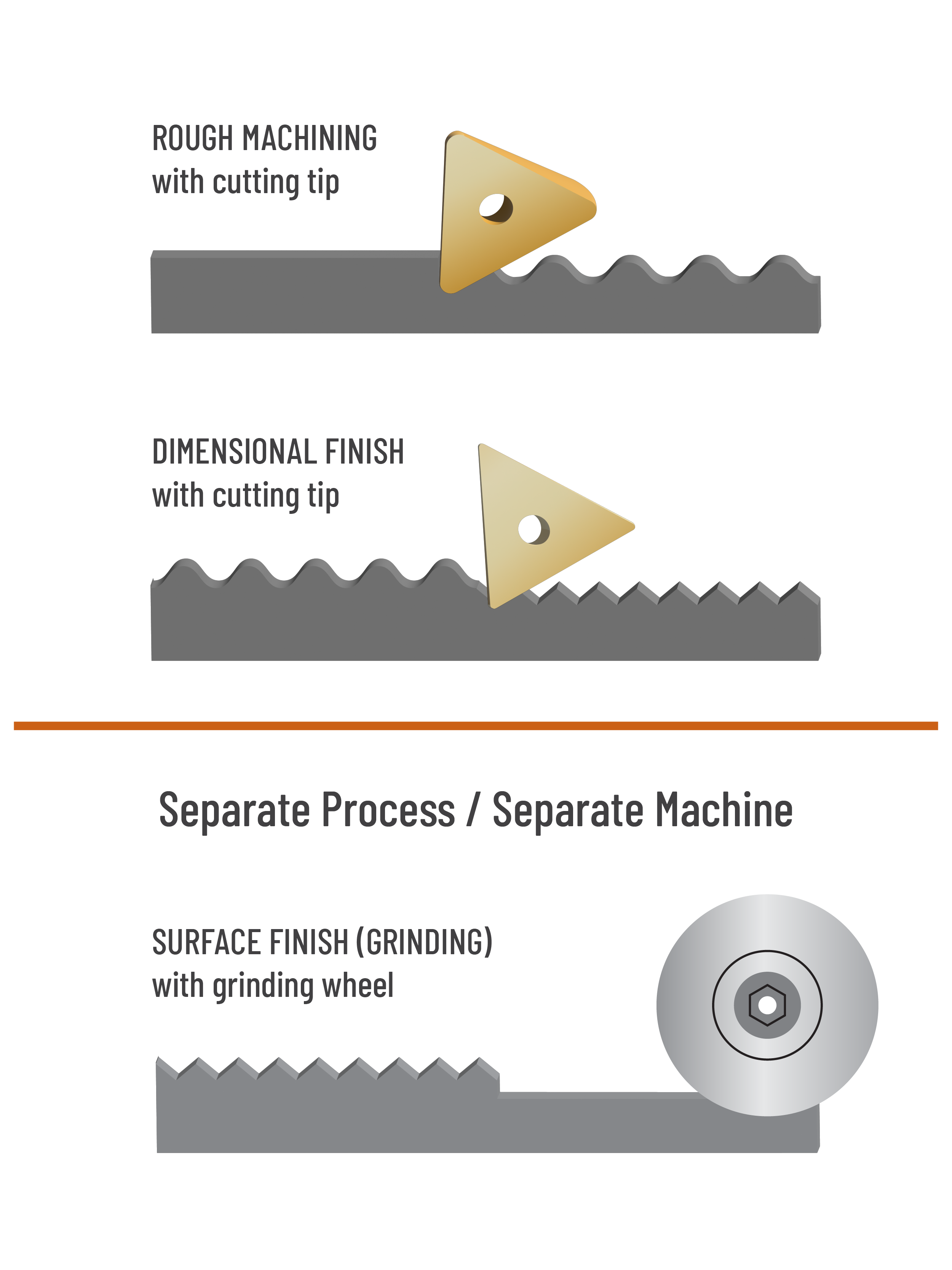
Lathe Machining with Superoll
Using Superoll, you can achieve the precise dimensional accuracy and surface roughness at the same time - and you only need to attach it in your lathe. No separate process needed.
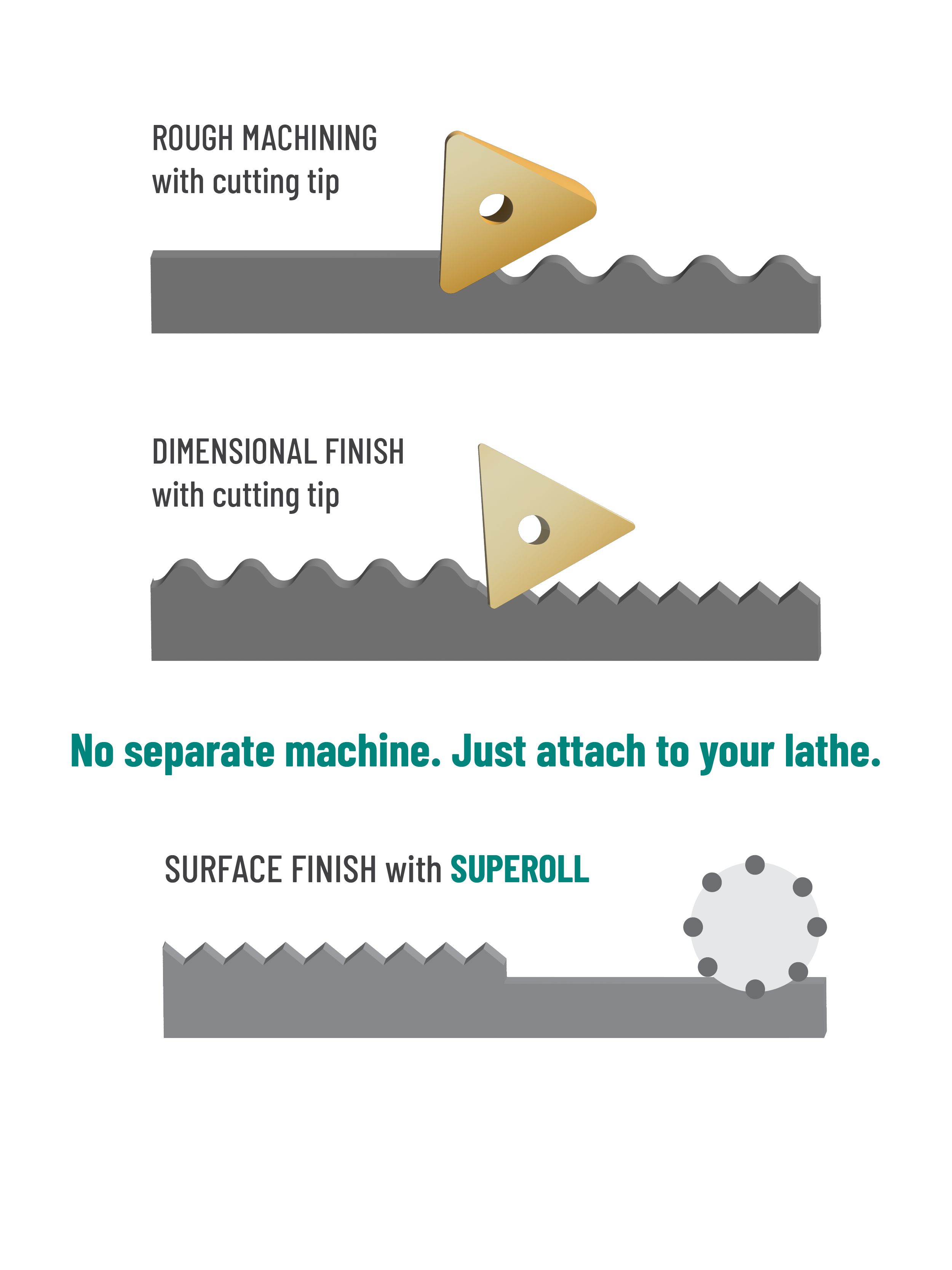
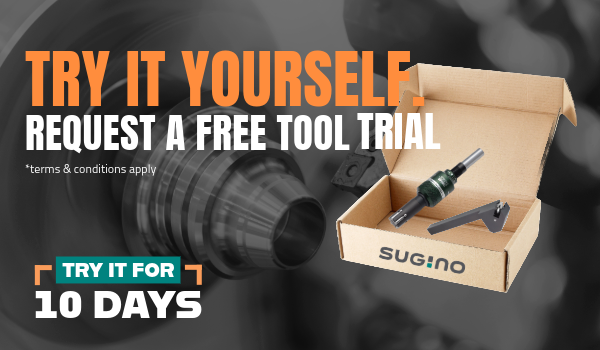
Try the Superoll Tool Trial
We're ready to help you find the right Superoll™ solution
Frequently
Asked
Questions
Single Roller Type - Product Lineup
SR5A
For shaft end surface
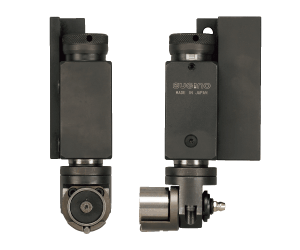
SR16M
For shaft end surface, taper, R surface
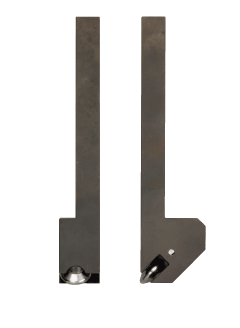
SR5C
For inner
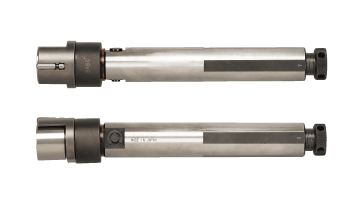
SR16C
For inner
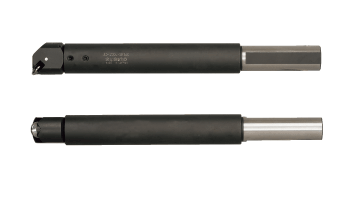
SR3Z
For outer groove side
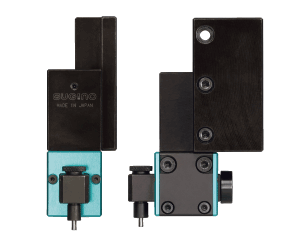
SR3ZH
For inner groove side
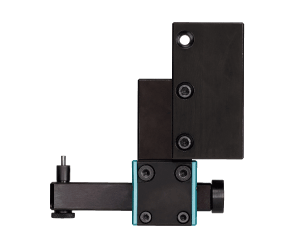
SR24MW
For outer groove bottom
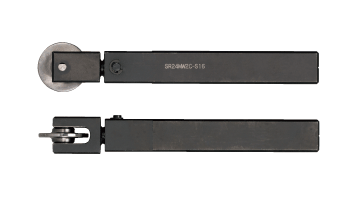
CEZF
For end groove surface
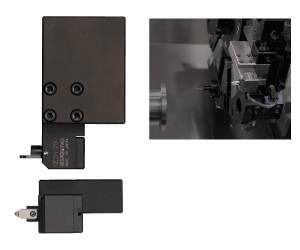
CEZH
For inner groove bottom
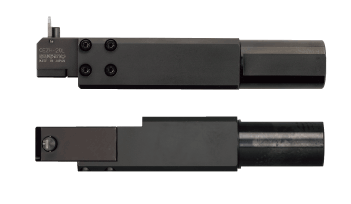
Materials
Acceptable Materials
Iron and non-ferrous material, including:
- Stainless
- SCM
- S45C
- FC
- ADC
- Copper
- Brass
Not For
- Titan
- Magnesium
- Wood
- Glass
- Ceramic
- Plastic